CIPAGEO®: Waterproofing and Lining
Waterproofing usually represents a small percentage of the total project cost. However, the wrong choice of materials for this segment can cause significant damage to a project. The technology used in the development and production of PVC geomembranes has undergone significant change and improvement in recent years. The use of new resins, plasticizers, additives and new lamination & finishing processes has made PVC an attractive and cost-effective alternative. These raw material improvements have resulted in a significant increase in the life of the product. Forensic analysis shows that PVC liners can maintain strength and flexibility for 30 years under certain conditions.
Why use PVC?
The PVC Geomembrane, due to its elongation which is greater than 300% (at a thickness of 0.75 mm) works practically within Hooke's Law, allowing it to support greater tensions caused by soil defor-mations, since it adjust to the soil deformation. In case the soil is compacted again, when the tension on the PVC is removed, the membrane practically returns to its original state. In the case of High Density Polyethylene, it has a transition point between the plastic state and the elastic state at around 15% elongation. It means that above that point the material no longer returns to its original state.
PVC, due to its amorphous structure, does not suffer from Environmental Stress Cracking, while the High Density Polyethylene, due to its crystalline structure, suffers from this phenomenon.
The E.P.A. - Environmental Protection Agency of the United States - recommends the use of at least 30 mil (0.76 mm) thickness for a PVC geomembrane and 60 mil (1,52 mm) thickness for a High Density Polyethylene geomembrane. Consequently, the impact on the material acquisition costs is signifi-cant.
Additionally, PVC is a geomembrane that is easy to transport, store and handle. PVC can also be factory welded and turned into panels, which can range in size up to 3,500 m² for a single panel. The user/in-staller gets an immediate return on the reduction of labor costs in the field, energy and transportation. Our field experience shows that twenty workers, in an 8-hour shift, can install up to 24,000 m²/day of PVC panels, without increasing the total cost of the job. This number, for example, for textured high density polyethylene, is 14,000 m²/day*.
* Cipatex internal analysis
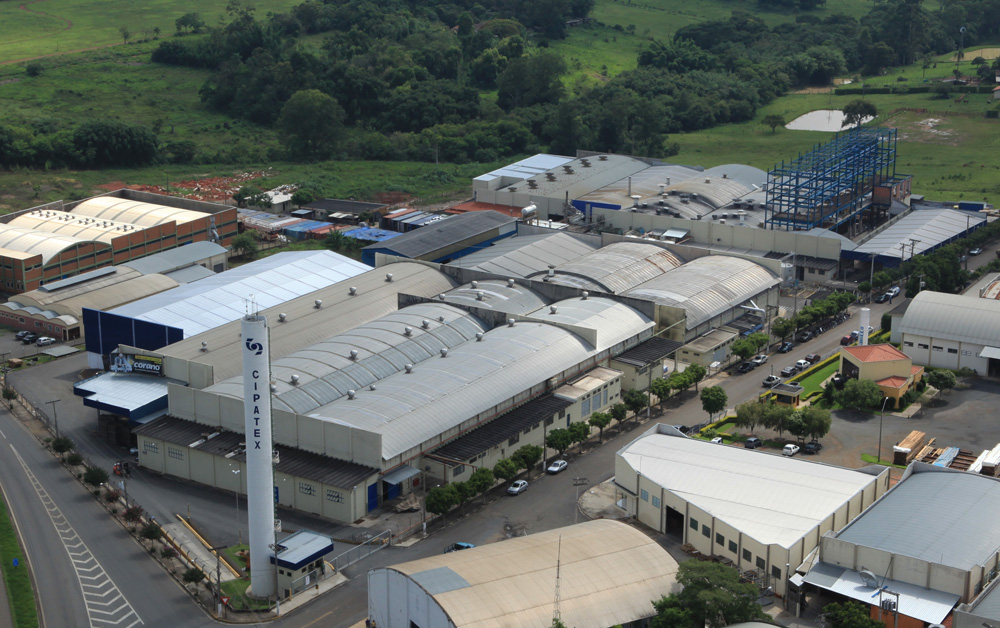